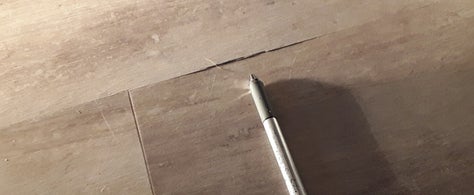
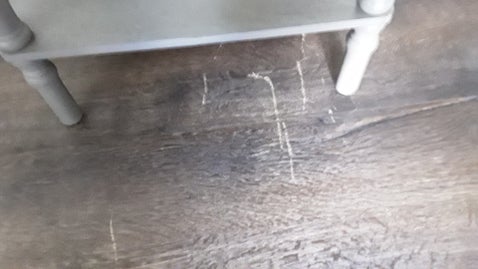
JL Camp Flooring, LLC
Flooring Inspections
Concrete Moisture Testing
Consulting
Bloomington, IL
(309)532-7230
jlcampflooring@yahoo.com
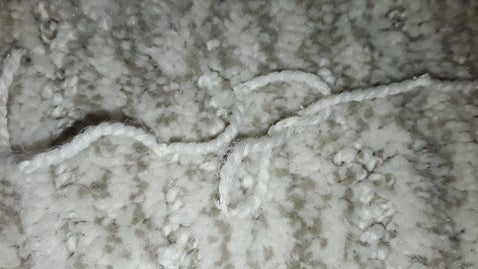
Residential and Commercial
About
J L Camp Flooring, LLC is a Bloomington, IL based flooring inspection company that provides professional and unbiased flooring inspections for Manufacturers, Retailers, Home Owners, Distributors and Installers/Contractors. Inspections include a detailed report outlining the flooring concerns, diagnosis of the problem, assignment of fault and corrective actions necessary for a satisfactory conclusion. When flooring projects become flooring problems call us.
Providing Flooring Inspections in the following areas
ILLINOIS
ST. LOUIS METRO
INDIANAPOLIS/EASTERN INDIANA
EASTERN IOWA
SOUTHERN WISCONSIN
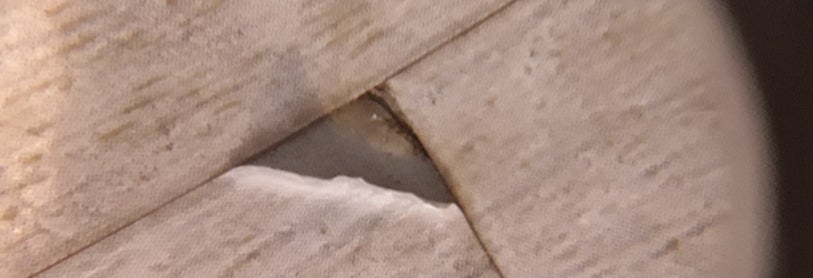
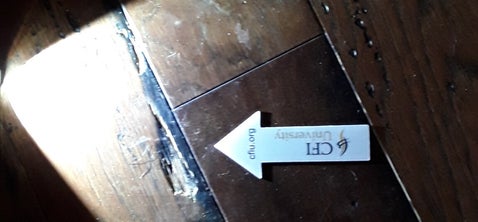
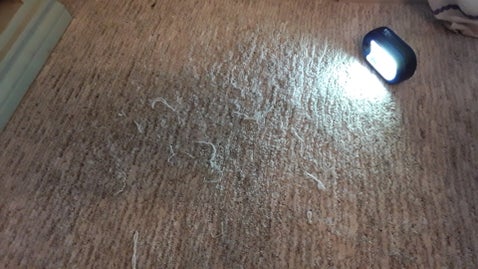
Providing inspections for the following flooring types
CARPET
HARDWOOD
LAMINATE
RESILIENT
BAMBOO
CORK
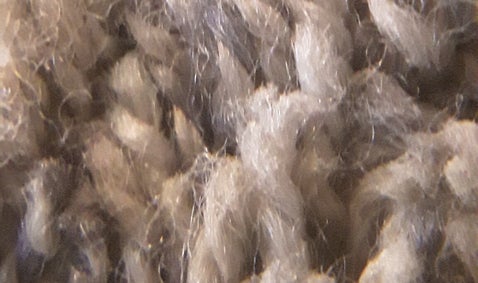
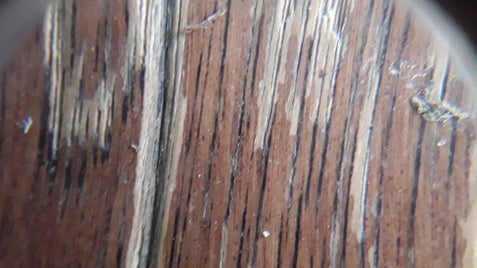
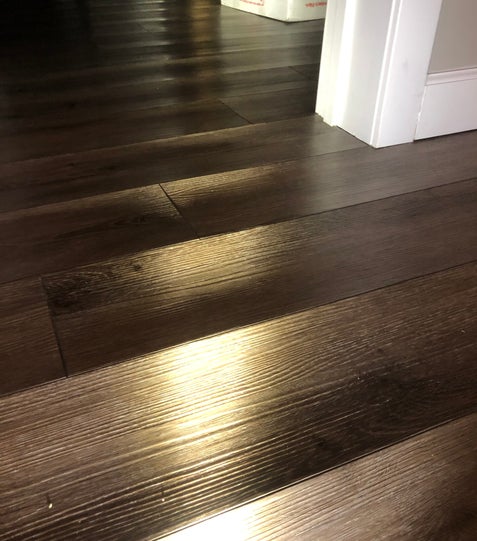
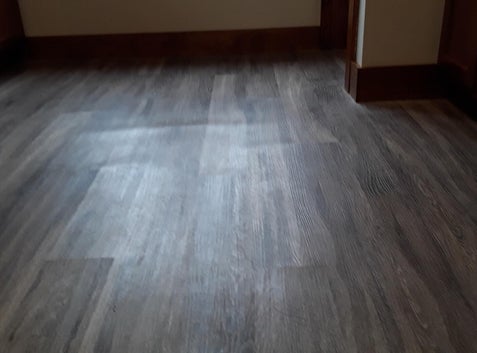
Additional Services
CONCRETE MOISTURE TESTING (ASTM F2170 and ASTM F1869 MVER) 3rd Party Testing and Verification
CONSULTING
SITE SURVEYS
REPAIRS (HARDWOOD, LUXURY VINYL, LAMINATE AND CARPET)
MICRO SHEARING CARPET TILES
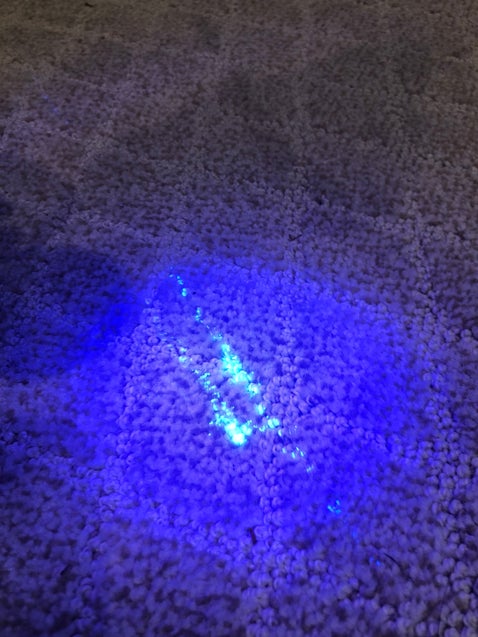
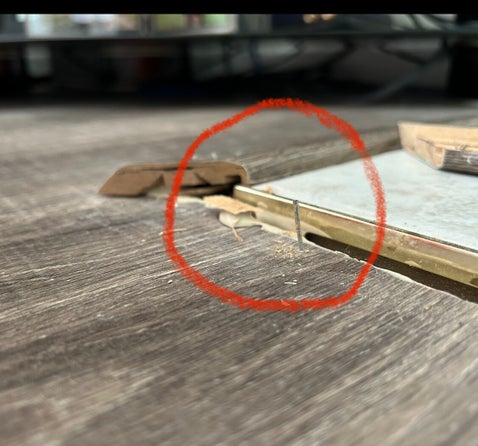
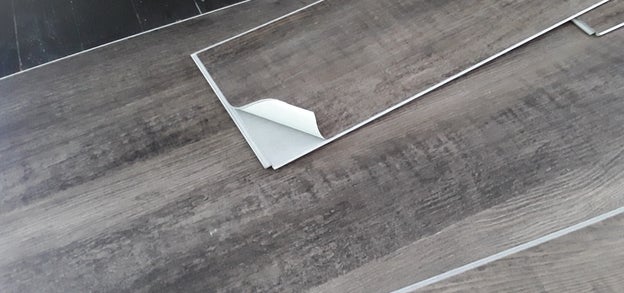
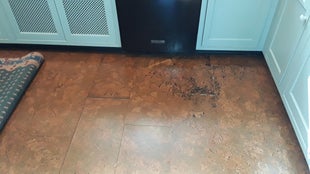
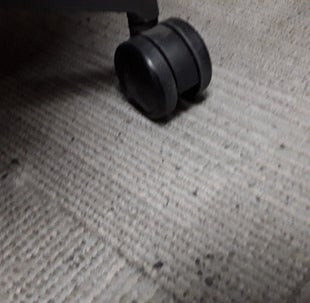
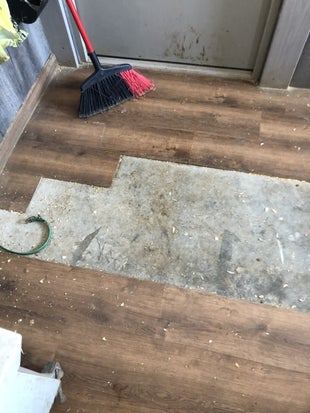
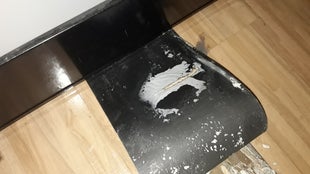
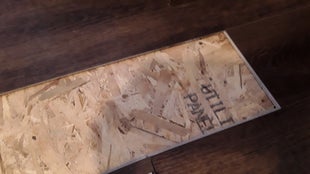
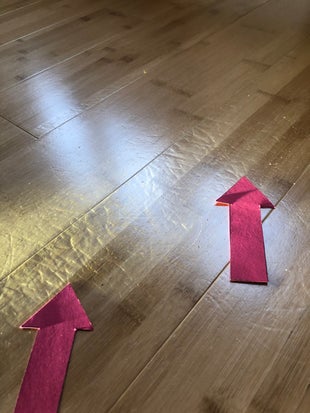
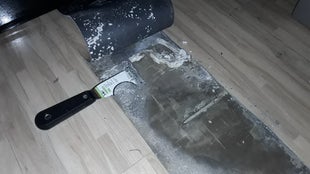
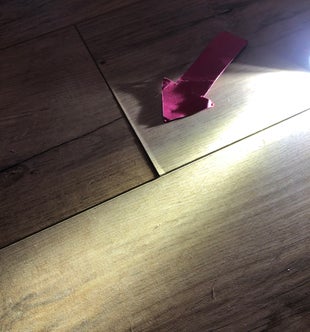
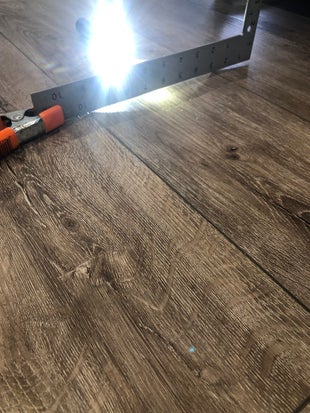
Curriculum Vitae
EXPERIENCE-
Flooring Installer (1988-2017)
Concrete Moisture Testing Technician (2017-Present)
Certified Flooring Inspector (2017-Present)
CERTIFICATIONS-
*Flooring Consultants and Inspection Training Services (FCITS)*
Dalton, GA
-Carpet Inspector School (2017)
-Hard Surface Inspector School (2017)
-Advanced LVT and Rigid Core Specialist (2019)
-Wagner Moisture Meters (Rapid RH Training Course 2020)
-Advanced Hardwood, Bamboo and Laminate Specialist (2023)
-Master Inspector Certification (2025)
ADDITIONAL COURSE WORK-
*Certified Flooring Inspectors University (CFIU)*
-Engineered Wood Course (2019)
-Luxury Vinyl Course (2019)
-Laminate Flooring Course (2021)
EVENTS/TRAINING-
FCITS Master Inspectors Expo (2017)
FCITS Inspectors Expo (2017)
FCITS Inspectors Expo (2018)
FCITS Inspectors Expo (2019)
FCITS Inspectors Expo (2020)
FCITS Inspectors Expo (2021)
FCITS Inspectors Expo (2022)
FCITS Inspectors Expo (2023)
FCITS Inspectors Expo (2024)
Mohawk Industries AIRO Carpet Installation Procedures (2018)
IFTI (Independent Floor Testing & Inspection) Field Technician Course (2018)
Congoleum ArmorCore Installation Procedures (2017)
CFIU Certificate of Participation- Gloss Meters, Luxury Vinyl, Ceramic Tile Cleaning Products, Report Writing (2022)
Wagner Moisture Meters Webinar, "The Why, What and How of Concrete Moisture Testing" (2023)
Wagner Moisture Meters Webinar, "The Why, What and How of Wood Moisture Testing" (2023)
MEMBERSHIPS/AFFILIATIONS/PARTNERSHIPS
Floor Detective
ASTM International
FCITS
FloorReports
Inside Edge Commercial Interior Services
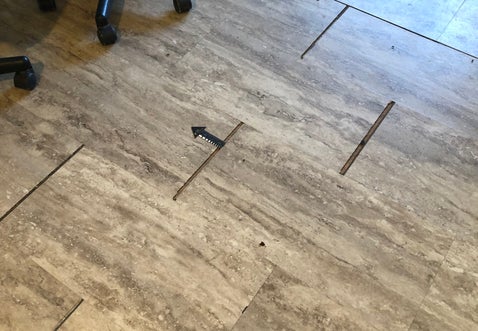
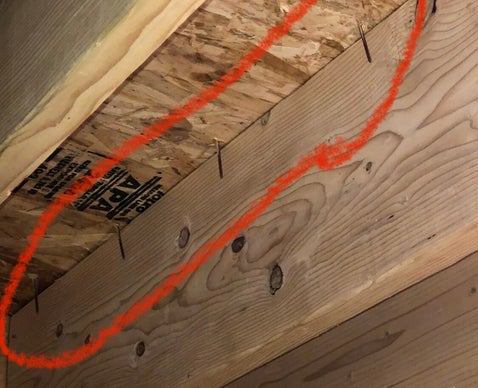
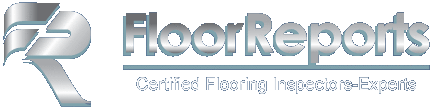
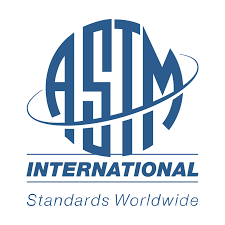
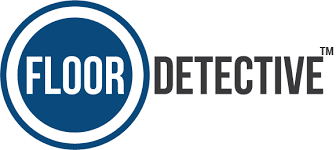
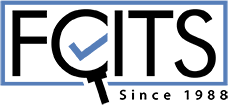
It’s no mystery. The leading cause of flooring failures is moisture.
Industry experts say approximately 85% of all installation failures result from moisture problems. In fact, moisture accounts for more than $1 billion in damages annually.
Moisture can cause a wide range of hardwood flooring problems that may occur soon after installation or, in some cases, months or even years down the road. These problems include cupping, buckling, blistering, crazing, adhesive failure or delamination, warping, scaling, pop-outs, efflorescence, discoloration, gaps or cracks, swollen joints, and even mold or mildew growth.
The reason moisture is the root cause of many flooring failures is simple. Concrete slabs, wood subfloors, and the wood flooring placed above a slab or subfloor are by their very nature porous. So they easily absorb and release moisture.
While it’s critical to ensure hardwood flooring reaches its equilibrium moisture content (EMC) with the air (that is, attain an optimum moisture level before installation), it’s equally – and perhaps even more – important to accurately measure the moisture content of the concrete. Why? Because moisture passing from or through concrete has become the number one cause of floor covering failures in this country.
For that reason, most U.S. producers of floor coverings, adhesives and resinous coatings require accurate moisture testing of both concrete and wood in order to avoid flooring failures.
It’s important then that flooring professionals have an understanding for the need of both concrete and wood floor moisture testing. They should also know the differences between the recognized concrete test methods and wood flooring moisture meters.
Concrete and Moisture
Concrete is porous material. The more porous it is, the greater the potential for moisture vapor to move at a volume harmful to the floor covering. Concrete slabs with a high moisture emission rate and/or too high a pH level will always be detrimental to a successful flooring installation.
Excess moisture in concrete can occur for various reasons and regardless of the age of the concrete slab:
- There may be too much water in the concrete mix
- Too little curing or drying time
- Rainfall from incomplete roofing systems
- Lack of HVAC climate control
- Poor landscaping that fails to drain water away from building foundations.
- Buffing the concrete smooth to iron out imperfections that may “telescope” into the floor covering. This practice hinders drying time because it seals the concrete’s pores.
High Alkalinity and Time
A related problem to excess moisture – too much alkali. High alkalinity destroys the bond between the adhesive and floor covering. High alkalinity occurs when too much moisture moves through the slab.
Alkalinity is a natural constituent of all concrete. The good: the internal alkaline state of concrete prevents reinforcing steel from rusting. The bad: when the surface of a concrete slab has an alkalinity above 9 on a pH scale (usually 10 and above), adhesive and bonding systems can be compromised.
To ensure concrete is at the proper state of alkalinity, testing with pH paper or a pH meter must be performed. Moisture causes damage, but moisture at a high pH is disastrous.
Still another problem is time. Many building contractors work on a fast-track construction schedule. As a result, concrete is not given enough time to naturally dry before installation of floor covering materials and coatings.
Making matters worse, is the use of curing compounds which inhibit or prevent concrete from drying . . . and the use of floor covering adhesives and coatings which are more sensitive to moisture and alkali assault than previous materials.
Keep in mind, flooring installers are attempting to adhere floor covering materials using water based adhesive systems to a water-based agglomerate called concrete. Excessive moisture emission from concrete that has not sufficiently dried will almost always interfere with the ability of an adhesive to bond or cure properly.
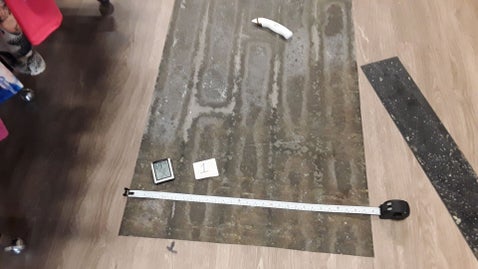
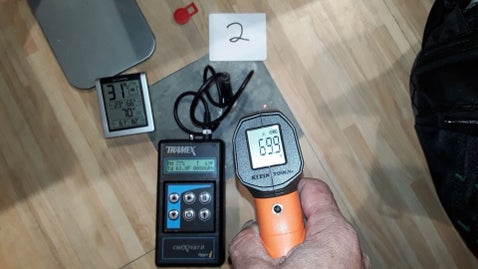
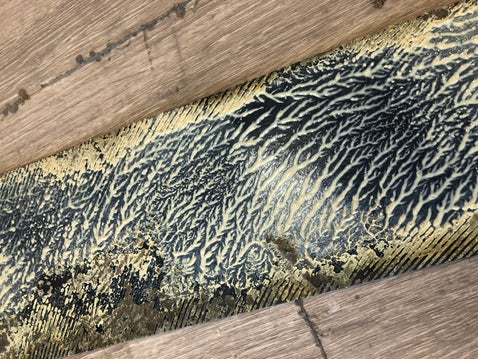
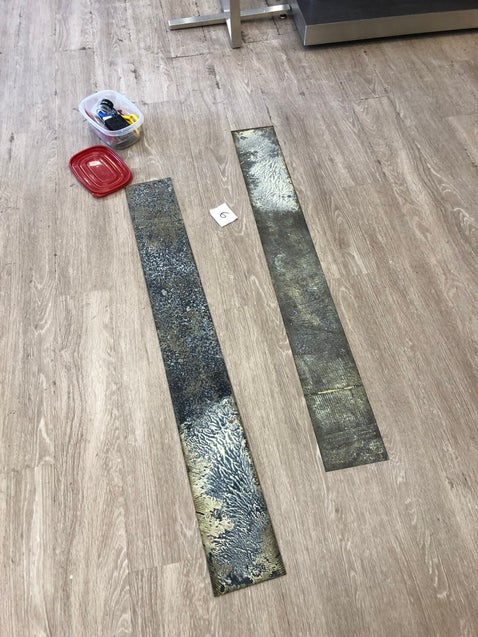
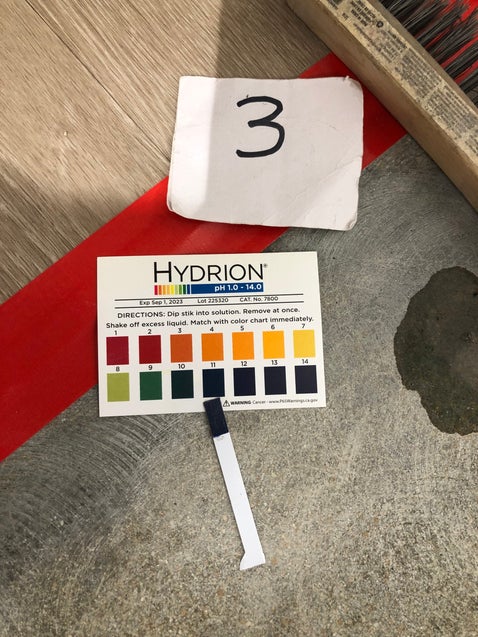
Floor Covering Problems
When a floor covering shows signs of moisture-related failures, the problem is likely due to one of the following;
- The concrete slab has a higher moisture emission rate than the floor covering can tolerate.
- The concrete was not cured or dried sufficiently before installation of the floor covering.
- No moisture testing was performed or it wasn’t done correctly.
- The moisture testing didn’t show future concrete slab behavior.
- Alkalinity is too high in the concrete due to a high moisture emission rate.
Alkalinity is measured by pH from 1-14. Ideally, concrete should have a pH of 7-9 before installing a floor covering; otherwise, the high alkalinity (high pH) combined with moisture will destroy flooring adhesive bonds.
Freshly mixed concrete is highly caustic and extremely alkaline – well above 10. This condition may compromise adhesives and flooring materials. As concrete ages and reacts with carbon dioxide in the air (part of the curing process), the alkalinity (or pH level) of its surface gradually decreases.
Before flooring is installed, the pH level of the concrete surface should be between 7-9. However, flooring installers should check the pH level recommended by the adhesive manufacturer as well as other manufacturers’ products that might be used on the subfloor, such as moisture barriers, epoxy coatings, and leveling compounds.
ASTM states that a pH test should be performed along with every moisture test. Many flooring manufacturers require pH testing be conducted before flooring is installed.
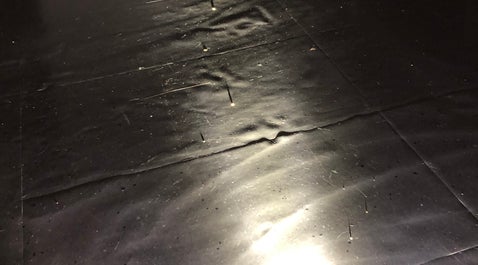
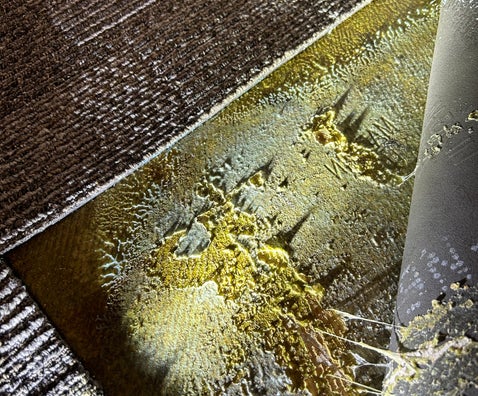
Types of Concrete Moisture Testing Performed
Anhydrous Calcium Chloride Moisture Tests, as described by ASTM F1869, measure MVER (Moisture Vapor Emission Rate) from the surface of the concrete slab, usually the top ½–¾ inch of the sample being measured.
In Situ Relative Humidity Probes, as described in ASTM F2170, measure at 40% depth of a concrete slab that is being dried on one side (top) or 20% depth of a concrete slab that is drying from two sides (top and bottom).
Non-Destructive Electrical Impedance Concrete Moisture Meters, as described in ASTM F2659, generally measure moisture content down to ¾–1 inch from the top of the concrete slab.
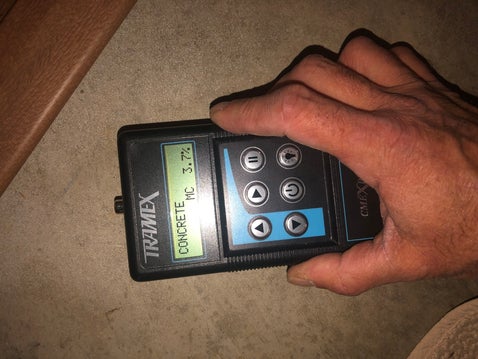
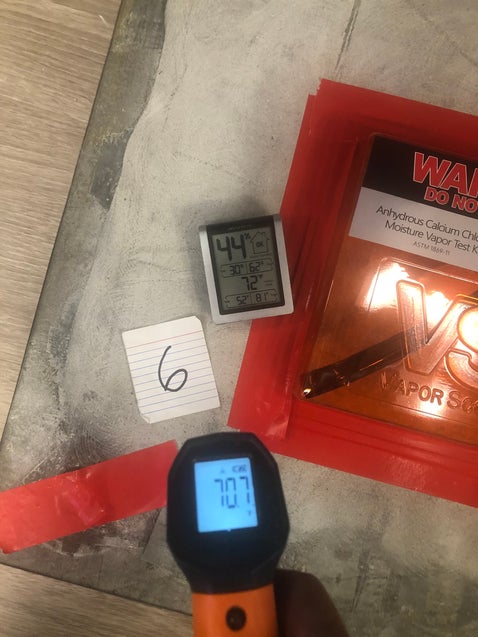
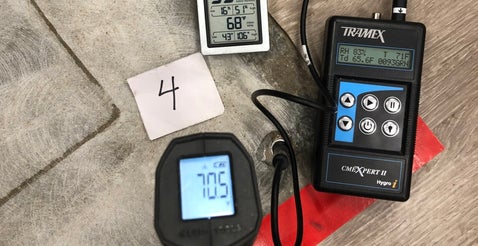
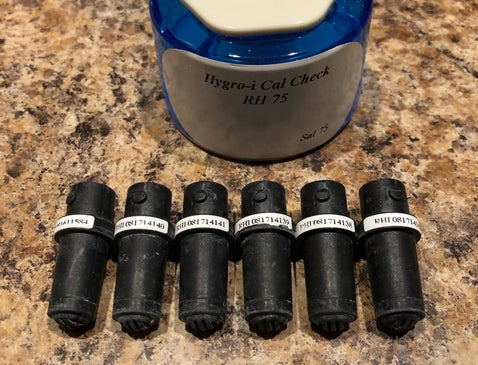
Wood Subfloor
Improper moisture conditions in a wooden subfloor can also lead to moisture related problems associated with a concrete slab. Flooring specialists can test the moisture content of a wood subfloor using the pinless moisture meter. Similar to the hardwood floor, the wood subfloor must have an acceptable moisture content to avoid flooring failures over time.
Flooring specialists should test several areas of a wood subfloor to be certain conditions are acceptable for the final flooring installation. A good rule of thumb is that the subfloor moisture content should be within 3-4 percentage points of the flooring to be installed before proceeding.
Wood Flooring
Regardless of whether hardwood or engineered flooring is to be installed, all material should be checked with an accurate wood moisture meter. This involves opening and testing several bundles to ensure the wood flooring is the same MC throughout, and is compatible with the subfloor which the flooring will cover when installed.
As with the wood subfloor, pin-style and pinless meters can give an indication of the MC to ensure a professional and long-lasting flooring installation.
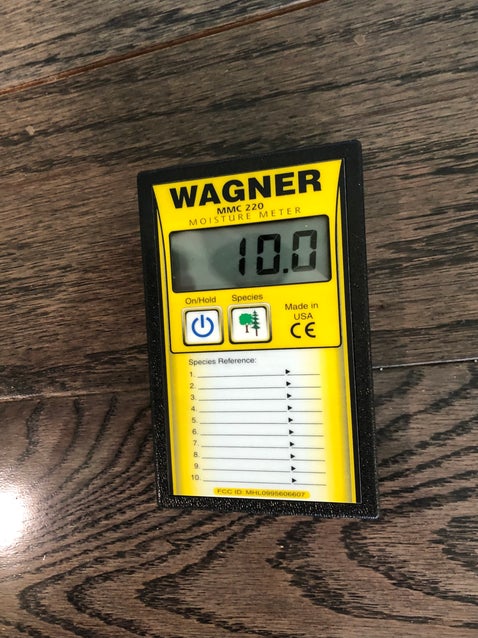
Source: Jason Spangler (Wagner Meters)